高炉炉缸结构上一些问题的讨论
汤清华
(鞍钢股份公司)
1 前言
高炉炉缸寿命的长短决定了高炉一代炉役的周期。高炉生产中只要炉缸不出现险情就可继续生产,炉缸以上干区无论出现冷却壁烧坏或炉皮开裂等毛病都可以通过短期的抢修来继续生产,有的还可修旧如新。而炉缸出问题则不行,一旦温度超限,采取措施不见效果,就必须停炉大修。因此,高炉大修周期由炉缸寿命来决定。
近年来我国高炉炉缸寿命得到大幅度地提高,出现一批10-19年的长寿高炉,也是以炉缸寿为评价的。长寿命为国民经济建设和节能减排做出了巨大的贡献。但发展不平衡,还有很多高炉达不到设计寿命,甚至不断发生炉缸烧穿事故,给企业安全、生产经营带来严重的损失。结合鞍钢新3高炉和国内外一些高炉炉缸烧穿的实际,提出延长高炉炉缸寿命结构上的一些的问题,与同仁共同讨论。
2 炉缸炉壳结构
2.1 一批1080m3高炉,开炉不久环炭温度急速升高,两年内多座高炉炉缸烧穿,数座被迫2年多一点就大修炉缸。图1是这批高炉的炉缸结构图,由图看出,这种炉缸是在早年低冶强低寿命的750高炉结构上,减薄炉衬演变而成的,炉缸炉壳是直圆柱筒,到风口上扩径成炉腹,这种结构极易造成炭砖上浮和砖缝变大,一旦占入铁水和Zn蒸气,进而环炭温度开炉不久就升高。究其原因,是个常识问题,炭砖的比重为1.55t/m3,而铁水比重是7.6t/m3,相差近5倍,这样铁水对炭砖起到向上浮动的推力作用, 炭砖不往上浮就得靠砖与冷却壁之间的磨擦力,这种磨擦力与铁水浮力方向相反,且那种力较大是显然可见的,好象一块轻质木头漂在水上一样。上世纪八、九十年代曾数次遇到高炉炉底炭砖整体漂浮而炉底烧穿的事故。正确的结构应从炉底板开始炉缸炉壳是个圆锥型,向上缩小,炉壳给炭砖一斜面的约束力,来限制炭砖上浮。大型高炉炉缸壳体基本上是圆锥型,中小高炉勿视了这个问题。
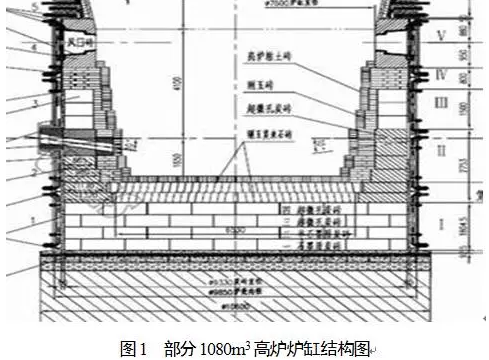
2.2 另一个问题是炉缸炉壳有一个内缩捌点来收缩,但收缩位置在风口段下方,太高,起不到作用,曾有数座1780m3高炉,开炉2.5年后温度急烈攀升近900℃或者烧穿,此结构如图2。有的同志认为:a.炭砖质量不好,b.施工质量差,c.冶炼强度过高,d.有害杂质超标。笔者认为不全面,这种炉壳结构不佳也应是原因之一。
为此建议凡新建或大修高炉,炉壳收缩变径只少应从炉底满辅炭砖中上部开始采取收缩,风口段有一段直段后至炉腹处再扩径,如果风口段砖衬太薄又易烧坏炉腹冷却壁冷面水管。很多实例让人们引起了重视。
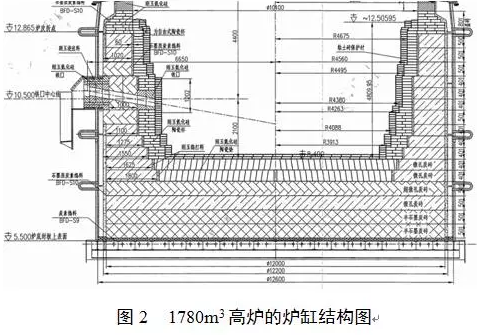
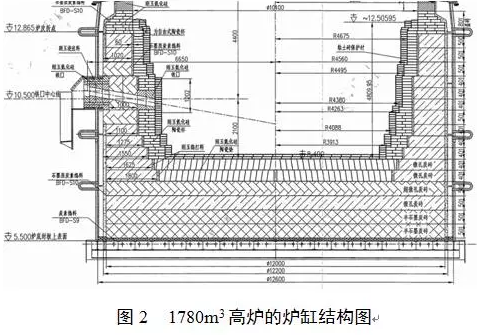
3 炉缸炭砖砖衬结构
3.1 炭砖厚度
图1、图2中炭砖厚度有的仅550mm,应当说太薄,薄炉衬是相对于传统的综合炉缸炉底来说的,不应只顾降低建设费用,15年寿命保证值与措施不对称。笔者认为微孔或超微孔材质的炉缸环炭炭砖厚度最薄处不应小于1000mm,炉底炭砖不能小于2000mm。某两企业的1780m3高炉,一张图纸下来的结构,同一家的超微孔炭砖,陶瓷垫处即象脚区炭砖厚200mm的炉子投产5年多出现该处温升高至600℃,而薄200mm的高炉开炉仅2.5年就升至近900℃。因此,减簿要有度。
3.2 大块炭砖砌筑的炉缸环炭应消除水平通缝
图1、图2大小两种结构的炉缸环炭结构的高炉,其大块炭砖无一例外都是水平通缝,这就造成铁水和Zn蒸气易占到靠近冷却壁处,插入300mm的电偶温度升高,或无先兆迹象的炉缸烧穿,这种结构的炉子我国居多,加之炭砖不断减薄,应引起行业的重视。无论那种砌筑建筑通缝都是不允许的,回头看似乎见怪不怪了,尤其是高炉这一高温高压容器必须高度重视。
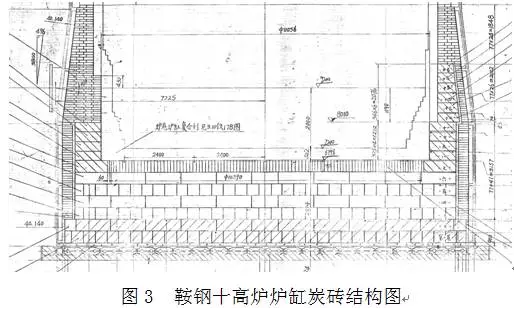
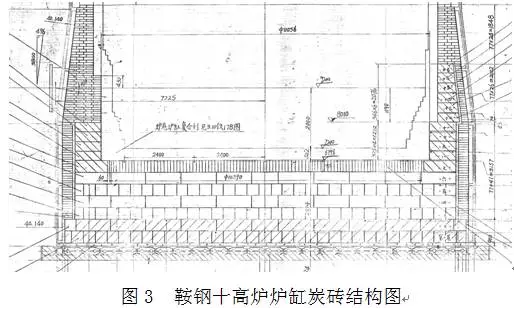
图3是鞍钢10高炉(2580m3)1995年2月12日投产时的设计图纸。这座炉子于2008年11月因金融危机被迫停下来,共生产了14年,单位炉容产铁10800t/m3.代,算是长寿高炉,冶强不低,前8年入炉品位仅56%,其后大修破损调查时,炉缸环炭最簿处仍有300mm。14年生产中炉缸没有任何温度升高等险情。由图可看出,20年前的炭砖质量远不如当今的好,但10高炉采用大块与小块炭砖复合砌筑,小块半石墨砖靠冷却壁砌筑,炭捣料层移至大、小块炭砖之间,进而消除了水平通缝,为鞍钢高炉长寿开创了好局面。因此当前全大块炭砖砌筑的水平通缝问题应加以优化。
3.3 坚持好传热的顺序
在炭砖等耐材结构上应坚持炉底砖衬由下至上,导热系数由大到小,环炉缸耐材应当冷面至热面导热系数也应由大到小,防止中间层的热量积累。目前尚有不少高炉做不到这点,有的甚至存在热阻层,炉内热量不能顺利导出,应切实做好。
3.4 高度关注炭捣料的材质与施工质量
我国采用大炭砖砌筑的高炉为消除三角缝,多在炭砖与冷却壁之间用炭素捣料捣实来实现热量传递,炭砖导热系为15w左右,铸铁冷却壁导热系多在35w水平,如果在冷却壁与炭砖之间的捣料层其导热系数小于15w,则形了阻热层,热量导不出去,炭砖层内温度就升高,应注意:1)炭捣料一定要做到在100-200℃时的导热系数大于其热面炭砖的导热系数。2)十分注重炭捣层的施工质量,400mm厚砖层捣料每次添加厚度应在100-120mm,捣实了验收了再添加上一层,再捣实。
有一企业6座1080m3炉子两年内烧穿3座,余砖衬温度攀升不敢再生产,大修时又无法调整炉壳收径问题,最终炭素捣料层改为浇注料,才解决这一问题,应努力开发高导热、价格低、易施工的浇注料。
4 冷却水与冷却器结构
4.1 冷却水质
水是最好耐火材料,这话不错,但应用得好。首先是水质,黄河以北地区的地表水硬度高,受热后暂时硬度淅出造成管壁内结垢,冷却器的冷却效果降低或失去了冷却作用,甚者水管堵塞,鞍钢工业水开路冷却的高炉,在上世纪八、九十年代经常出现新高炉开炉半年就结垢堵塞水管,因此不能直接引用。应变成软水或除盐水(工业纯水。软水应有防腐,除盐水要有脱氧措施)。长江、珠江流域水质硬度低一些,但近年来硬度也上升到220左右,因此高炉冷却水建议不再直接采用工业水,应加以处理后才能应用,尚有不少企业对此缺少认识和监控。
4.2 冷却壁与冷却比表面
先举例子,鞍钢新3高炉与宝钢3、4高炉,这3座高炉炉缸所用耐材及结构为一家生产的,都是小块炭砖结构。宝钢3高炉创造了19年长寿命的典范,而鞍钢新3高炉开炉2.7年就发生了炉缸烧穿事故。宝钢4高炉,它与他们厂的3高炉也是同一家的耐材及结构,且炉缸用了二段铜冷却壁,但4高炉也只生产了9年,因炉缸环炭温度高被迫在2014年9月对炉缸进整体移装的办法进行大修,而风口以上则不用捡修,停炉破损调查炭砖最薄处不足300mm,低于运行19年的宝钢3高炉。
是什么原因造成这么大的差别?宝钢3、4高炉其操作水平、冶炼强度、用料结构及稳定性、施工质量等可以说应当是相同的,国内外属一流,也找不出不足之处。差在什么地方?表1中列出三座高炉的冷却壁结构及冷却比表面积
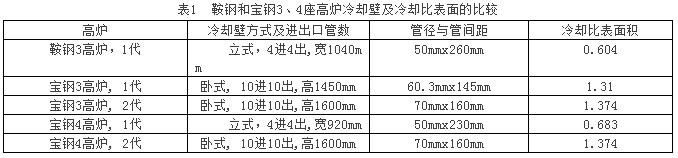
(1)宝钢3高炉的冷却比表面积是宝钢4高炉第一代、鞍钢3高炉第一代的两倍多,表明炉缸铸铁冷却壁的冷却比表面积0.6以上是不够的,宝钢4高炉第一代只能运行9年应当说这是结点,同样某5800高炉炉缸立式冷却壁冷却比表面积做到0.98,虽不断增加水量但环炭温度仍难于控制,因此建议学宝钢3高炉做到1.3以上,宏观上的低水量,微观上的高冷强。
(2)卧式冷却壁既保证了炉壳开孔处的强度,又均匀了冷却水温,宝钢4高炉第一代不单炉缸环炭温度不能受控,压浆还造成炉壳变形,因此,第二代则采用了宝3高炉的结构,应为成功的经验。
(3)宝钢4高炉炉缸第一代用了2段铜冷却壁,实践说明炉缸用铜冷壁没达到长寿的目的,在此再次建议若非要采铜冷壁“湿区”也不宜采用钻孔机加工铜冷却壁,每块冷却壁12-16个焊接孔,在炉内受各种应力一旦开焊渗水,将造成恶性事故,宜用铸铜冷却壁。
(4)接近20m直径的炉壳内,每1.6m高度上安装卧式排列20块冷却壁,较好地做到了每块冷却壁10进10出的冷却水管,冷却表面是当今冷却壁结构炉缸最大的,虽然水量偏小但流速达到1.8-2.0m/s。
(5)上述所谓”冷却比表面积”与炉缸外面喷淋冷却、夹壳式冷却方式不同,我国行业内是用冷却水管外周长再除管间距,即冷、热表面都计算进去了,与前两种结构进行比较应除以2才可相比。
因此,用此例来讨论当今炉缸冷却壁的优化问题。
4.3 冷却水量与水速
上述3.1-3.2中所说的水质和冷却比表积满足要求后,就是水速高低和水量的匹配问题。
(1)笔者认为水速应保证2.0±0.2m/s,这是生产中验证了的,主要防止冷却壁局部过热而出现的汽塞现象,尤其是闭路循环冷却系统。传热理论上计算上尚可低一些,但考虑炉役后期强化冷却及安全系数余力应不能低于这个数。
(2)水速和冷却比表面积都做达到要求,水量就确定了,闭路循环是省水的但循环用水不省电。
(3)此时如再采用分段式冷却,总水量是增加的,这就应优化匹配,学习武钢的联合循环冷却系统。
(4)表2例出卧式冷却与竖排立式冷却壁达到同样水流密度的比较,这是宝钢同志根据他们情况计算结果,供参考。表中的同样达到119的水流密度,立式冷却壁只能在冷却比表面积上下功夫,4.0m/s水速其系统要整体升级。

5 关于死铁层深度
死铁层深度为炉缸直径20%不宜继续加深,有不少实例证明,过深不一定使炉缸长寿和减少象脚侵蚀,目标是炉缸形成锅底型侵蚀。如某1250m3高炉,死铁层设置为2800mm,无陶瓷杯壁,按炉缸直径20%应当是1600mm,开炉4.5年因锌害环炭温度升至1080℃,被迫停炉大修炉缸,结果炉缸侵蚀最严重的处仅剩280mm,且从陶瓷垫表面上移了1400mm左右,也就是说加深的死铁层不但没起好作,反而造炉底温度过低,炭砖中占入大量Zn,形成Zn板,将炉底板平均抬高1200mm。建议再实践几年,并提出几个讨论问题。
(1)死铁层加得过深后,铁水高静压力与铁水渗炭速度的影响,
(2)死铁层加深理论上说明减少环流和实践的证据有待再探讨,
(3)过去高炉多为单铁口高炉和大渣量冶炼,为了怕两次铁间风压升高,而逐渐提高到20%炉缸
直径的死铁层深度,而当前多数高炉为多铁口,出铁间隔短或无间隔出铁,其环流路经和速度都发生变化,直得重新分析,
(4)死铁层过深对形成锅底形炉缸侵蚀有利与否和对加深铁口深度维护有利与否也值得探讨。
6 结语
笔者应高炉年会的要求,为实现高炉炉缸高寿命,仅在炉缸结构上就近年生产中遇到的一些问题,与同仁们进行探讨,提供给决策和设计者作参考,个人认识不一定正确且分析较肤浅,目的是想引起争议和引玉的作用。
7 参考文献
[1] 汤清华.延长高炉炉缸寿命一些问题的再认识.炼铁,2014.vol.33.NO.5.P.7-11.
[2] 王宝海,谢明辉. 鞍钢新3号高炉炉缸炉底破损调查. 2012年炼铁学术年会文集,中国金属学会,p32-38.
[3] 汤清华.高炉炉缸炉底烧穿事故分析及解决对策. 鞍钢技术,2012(3),p1-6.
[4] 陈永明,林成诚.宝钢3号高炉高效长寿技术.2012年炼铁学术年会文集,中国金属学会,p39-45.